December 17, 2023
Experience the transformative era of mobility characterized by digitalization, powertrain electrification, and autonomous driving. As the demand for electronic components rises in this dynamic landscape, ensuring their protection becomes paramount—an element that can be a literal lifesaver. The reliability of these components hinges on the precise application of essential sealants, adhesives, potting compounds, and thermal management. These elements play a critical role in safeguarding the integrity of electronic systems.
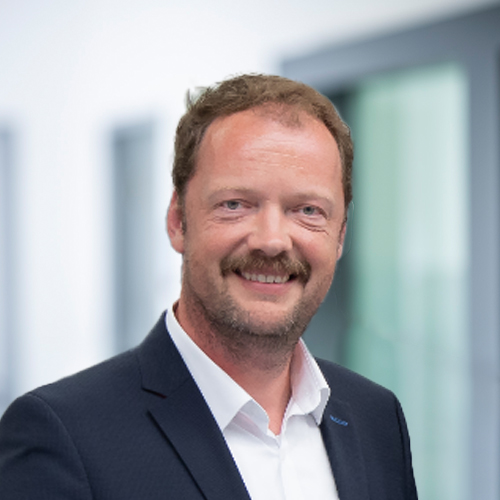
“It is important to protect sensitive e-mobility components, assistance systems, sensors, and assemblies against environmental influences. These are for instance high temperatures, dirt, moisture, and strong vibrations. The right dispensing and potting technologies prevent costly defects and failures. This may mean the difference between life and death.”
Marc Heiter E-mobility expert of Scheugenpflug Electronics Dispensing, Part of Atlas Copco Group
Importance of sensors in cars especially electric vehicles
Electric vehicles include many sensors, such as radar, parking distance, TMAP (Test Management Approach), ultrasonic, and image sensors. Safeguarding these electronic systems is extremely important to ensure electric vehicles' correct and safe operation. Sensors are protected through bonding, sealing, or potting with the help of varying viscosities. Housing contacts are shielded from harmful effects using appropriate bonding or potting materials. Given the diverse requirements based on sensor type, position, geometry, and function, no universal material is suitable for all applications.
Three topics to look out for protecting sensitive sensors and electronic equipment
- 1. Staying cool
- 2. Staying hidden
- 3. Staying failure free
Staying cool:
To avoid defects and failures in electronic equipment the heat they generate must be reliably dissipated. Dispensing accuracy, speed of application, and the wear and tear of the dispensing systems play a key role here. This applies in particular to dispensing for inductive charging stations, HV batteries, control units, onboard chargers, and Advanced Driver Assistance Systems (ADAS). Thermal management is also essential for power electronics as these components generate heat. Dissipating high temperatures supports the components to operate safely.
How to control airtightness of electronic equipment
Housings for electronic components have to be airtight. Absolutely airtight!
This is the last and most important step before the electronics are installed in the vehicle. Vision systems support perfect control of the airtightness of the components. They are inspecting these critical sealing applications. Our vision systems ensure that the quality of the sealing contour is exceptional, verifiable, and traceable.
E-mobility meets sustainability
Certainly, the global production of electric vehicles is set to surge, reaching approximately 35.7 million units by 2030 necessitating a proportional increase in sensors. The focus will shift to innovation, weight reduction, efficient supply chains, and minimizing the carbon footprint. Stakeholders are increasingly seeking transparent evidence of environmental impact.
Enhanced dispensing precision reduces material requirements, while advanced feed technology diminishes residue. Improved protection extends the lifespan of electronics, contributing to sustainability, safety, and reliability.